AL-6XN® Alloy
For high chloride and high temperature applications. Solve serious corrosion problems with AL-6XN® hygienic tubing and fittings.
Solve Corrosion Problems for Sanitary Piping Systems
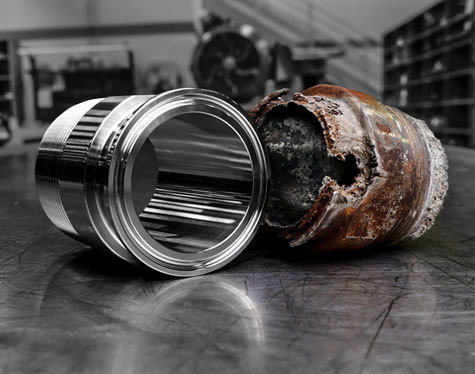
CSI has responded to the market demand for corrosion-resistant alloy tubing and fittings in high purity and sanitary process systems by maintaining extensive stock of AL-6XN®. This assures quick turnaround of projects.
AL-6XN (UNS N08367) provides a stable and reliable value that enables the owner to establish an accurate return on investment. Decreases in unplanned downtime, product loss, and maintenance costs with AL-6XN contribute to this value.
AL-6XN alloy is identified by the Unified Numbering System (UNS) designation of N08367. It is an austenitic stainless steel alloy with high nickel (24%), chromium (22%), molybdenum (6%), and nitrogen (0.18%) content and is commonly known as superaustenitic stainless steel (alloys such as 254 SMO (UNS S31254) and 904L (UNS N08904) also fall under the superaustenitic designation) while 2205 (UNS S32305/ S31803) and 2507 (UNS S32750) are duplex and super duplex stainless steel, respectively.
WHY AL-6XN®?
AL-6XN is widely used because it is a 6% moly superaustenitic alloy providing strong resistance to chlorides found in ketchup, barbecue sauce, sports drinks, buffer solutions, and active pharmaceutical ingredients that commonly cause localized corrosion.
AL-6XN is an upgrade to 300 series alloys such as 316L/1.4435 and 304 when high concentration of chlorides, high temperature, acidic pH levels, and time of contact are introduced to the process. This alloy is recognized by the ASME BPE standard, which identifies several specifications in Part MM (Metallic Materials) and by U. S. Food and Drug Administration (FDA).
1. GOOD MANUFACTURING PRACTICE
Choosing the right sanitary equipment and materials to avoid corrosion is a best practice for most processing environments.
2. NO MICROBIAL CONTAMINATION
No crevice and pitting corrosion, no product accretion.
3. PRODUCT AVAILABILITY
CSI Stocks over 65,000 feet of tubing and thousands of fittings.
4. AVOID EQUIPMENT REPLACEMENT
Super Alloys provide a good return on investment by reducing product loss and maintenance time repairing and replacing corroded parts.
AL-6XN® ALLOY ADVANTAGES
Why use AL-6XN alloy? Corrosion resistance, cost-effectiveness, and availability are just a few of the many reasons.
AL-6XN alloy is very attractive to many industries, because it is resistant to a broad range of corrosive environments and provides a high return on investment. The biggest advantage is CSI's availability and large stock to address your high corrosion resistance requirements.
1. CORROSION RESISTANCE
Corrosion in the forms of pitting, crevice, and stress corrosion cracking in 304 and 316 stainless steels are often better managed with AL-6XN alloy. This alloy is resistant to corrosion from various acids, salt solutions (sodium chloride) in hot and cold environments.
PREN
The Pitting Resistance Equivalent Number (PREN or PRE) is used as a guide for comparing and ranking a material’s corrosion resistance. The PRE Number is calculated from a formula based on chemical composition.
In today’s market, there is a wide range of austenitic, superaustenitic, duplex, superduplex, and nickel-based alloys. Besides corrosion resistance, other factors should be taken into consideration, such as commercial availability, appearance, good mechanical properties, and fabrication characteristics.
Alloy | UNS | EN Number | Cr | Ni | Mo | N | PRE Number | |
---|---|---|---|---|---|---|---|---|
316L | S31603 | 1.4404 | 16.5-18.5 | 10.0-14.5 | 2.0-3.0 | 0.1 | 23 | Austenitic |
S31603 | 1.4435 | 17.0-19.0 | 12.5-15.0 | 2.5-3.0 | 0.1 | 26 | Austenitic | |
904L | N08904 | 1.4539 | 19.0-23.0 | 23.0-28.0 | 4.0-5.0 | 0.1 | 34 | Superaustenitic |
2205 | S32205 | 1.4462 | 22.0-23.0 | 4.5-6.5 | 2.5-3.5 | 0.14-0.20 | 35 | Duplex |
2507 | S32750 | 1.4410 | 24.0-26.0 | 6.0-8.0 | 3.0-5.0 | 0.24-0.32 | 42.5 | Duplex |
254SMO | S31254 | 1.4547 | 19.5-20.5 | 17.5-18.5 | 6.0-6.5 | 0.18-0.25 | 42 | Superaustenitic |
AL-6XN | N08367 | - | 20.0-22.0 | 23.5-25.5 | 6.0-7.0 | 0.18-0.25 | 43 | Superaustenitic |
Maximum, unless range or minimum is indicated. Values listed are primary elements only and are not complete chemical compositions as listed in specific product type specifications.
GENERAL NOTES: The following are industry-accepted formulas. Other formulas may be used at the owner’s discretion.
For stainless steels: PRE Number = %Cr + 3.3 [%Mo + 0.5(%W)] + 16(%N)
2. Cost Benefit
Corrosion is an expensive problem but can be prevented. If the process solution and manufacturing process cannot be modified, the selection of the right material is the next step.
Some of the direct and indirect factors to consider when doing a return on investment calculation:
Direct losses
- Material cost
- Maintenance cost (repair or replacement)
- Overdesign
- Service life
Indirect losses
- Microbiological contamination
- Production shutdown
- Product loss (leakage)
- Safety of the employees (equipment failure and accidents)
- Environment clean up
It is also a cost-effective substitute to non-metallic materials such as PVDF, PTFE, TPE, or PVC because of special equipment and techniques during installation as well as the additional support required to not deform the polymer when in process. AL-6XN uses the same welding technique as 316L.
3. Product Availability
Allegheny Technologies Incorporation (ATI) AL-6XN is covered by ASME and ASTM specifications associated with the various alloy products forms.
This material is acceptable for use per “Part MM” (Metallic Materials) section of the ASME-BPE international standard and US Food and Drug Administration (FDA), and National Sanitation Foundation (NSF).
Product Forms |
---|
Plate |
Sheet |
Strip |
Billet |
Round Bar |
Wire |
High Purity and Sanitary Tubing |
Pipe |
Components |
---|
High Purity and Sanitary Fittings |
Pipe Fittings |
Pumps |
Valves |
Fasteners |
Castings and Forgings |
Spray Balls |
Instrumentation |
Strainers |
Adapters |
Specialty Fittings |
Piping Spools |
AL-6XN INDUSTRIES & APPLICATIONS
AL-6XN alloy has a long history in food, beverage, dairy, personal and home care, and biotech and pharmaceutical applications.
Processes such as buffer solutions, saline solutions, API, ketchup, liquid eggs, soy sauce, sports drinks, deodorant/antiperspirant, shampoo, liquid soap, and detergent, contain a high percentage of chlorides. In some cases, the product may not be corrosive but the clean-in-place (CIP) cleaning chemical is affecting the entire system. AL-6XN alloy is an excellent choice in instances where 316L/1.4435 and 304 stainless steels do not meet corrosion-resistant standards.
Select an industry or application to learn more
Biotech and Pharmaceutical
- Buffer Solutions
- Chromatography Columns
- API
- Saline Solutions
- Ethanol Distillation
- Oral Rehydration Salts (ORS)
Personal Care
- Shampoo and Conditioner
- Toothpaste
- Deodorant/Antiperspirant
- Body Wash
- Liquid Soap
Home Care
- Fabric Softener
- Detergent
- Cleaning Supplies
Food, Dairy, and Beverage
- Condiments: Ketchup, Salsa, Mayonnaise
- Sauces: Tomato, Soy, Barbecue, Fish, Chili
- Breaker Eggs/Liquid Eggs
- Soup Stock
- Brine Solutions
- Isotonic Drinks
- Cheese
- Vinegar-based Products
CSI Standards
All AL-6XN tubing and fittings supplied by CSI shall be provided to the following criteria.
Tubing and fittings are in stock in sizes 0.5” to 4”
SURFACE FINISH OPTIONS
The finish designator is indicated in the CSI item number as a suffix. The suffix will define the finishing requirements for the process component and tubing.
BPE Surface Finish Code | CSI Surface Finish Code | Product Contact Surface
(Max Ra)* | Product Contact Surface Finish Treatment
(ID) | Non-Product Contact Surface
(Max Ra) | Non-Product Contact Surface Finish Treatment
(OD) | Dimensions & Tolerances (BPE) or (CSI) |
---|---|---|---|---|---|---|
N/A | PU | N/A | Unpolished/Mill | N/A | Unpolished/Mill | CSI |
N/A | 7 | 32 µ-inch (0.81 µm) | Mechanical Polish / As drawn | 32 µ-inch (0.81 µm) | Mechanical Polish | CSI |
SF1 | PL | 20 µ-inch (0.51 µm) | Mechanical Polish/As Drawn | 32 µ-inch(0.81 µm) | Mechanical Polish | BPE |
SF5 | PO | 20 µ-inch (0.51 µm) | Electropolished | 32 µ-inch(0.81 µm) | Mechanical Polish | BPE |
SF6 | P25 | 25 µ-inch (0.64 µm) | Electropolished | 32 µ-inch (0.81 µm) | Mechanical Polish | BPE |
Welding AL-6XN Alloy
AL-6XN alloy is easy to weld using similar parameters as Type 316L stainless steel, including travel speed (IPM) and weld current. It is common to use a weld insert ring for additional alloying when orbital or manual welding in the field.
We've outlined a complete guide to AL-6XN welding recommendations in the resource below.
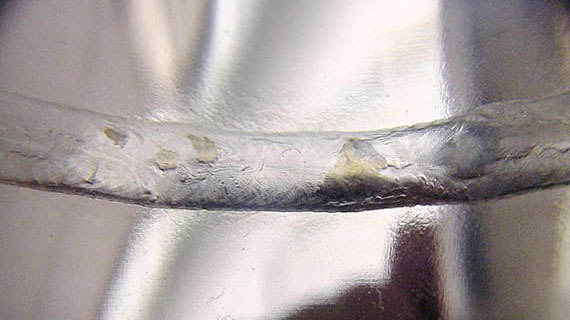
Weld appearance can be somewhat misleading when visually compared to hygienic welds made in 316L stainless steel. A typical AL-6XN weld has non-uniform freeze lines and oxide islands in the weld bead. These oxide islands appear as a thin film, having a varying color with tints from gray to dark brown that adhere to the surface. The appearance of “light” and “dark” spots on both the inside and the outside of the weld is typical. The heat-affected zone (HAZ) can also have discoloration and is generally a little darker than conventional 316L welds.
AL-6XN Videos
Alloys Case Studies
The True Cost of Pitting Corrosion
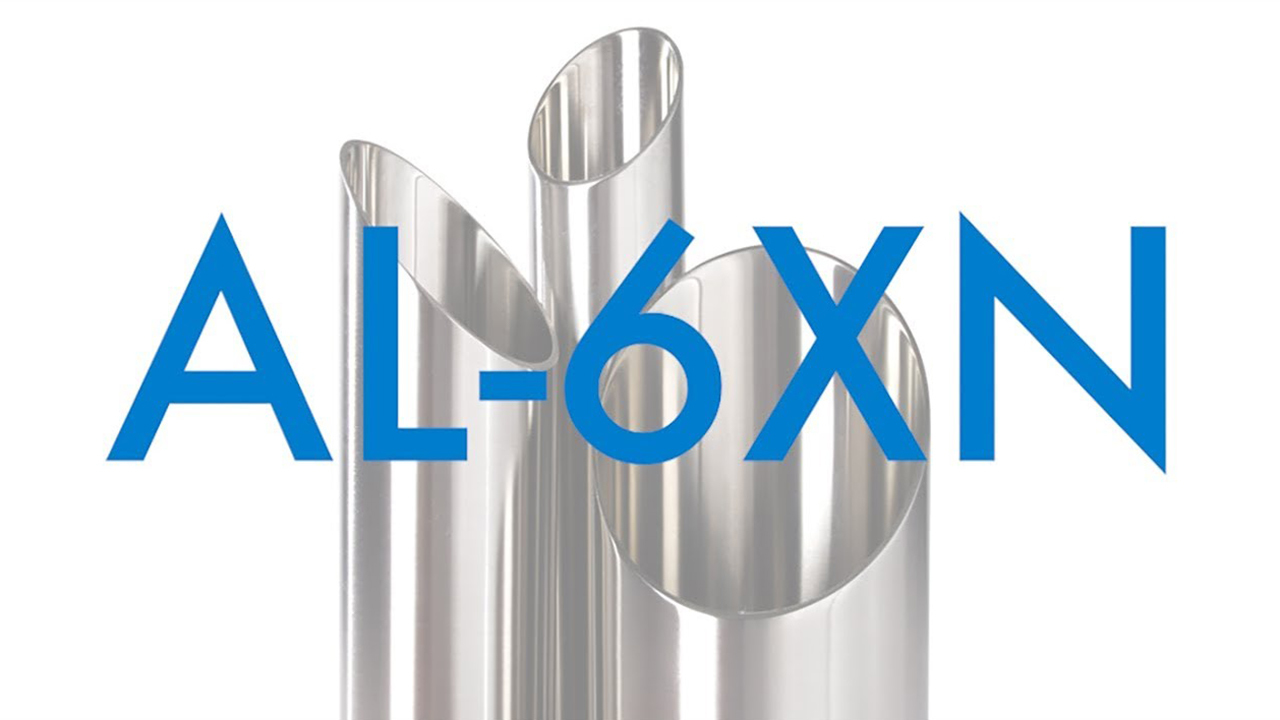
A deodorant manufacturer replaced their 316L piping 3 times in under 3 years. They contacted CSI to find a solution to their problem. CSI recommended replacing their pipelines with AL-6XN, which would provide better resistance to the facility's process.
Evaluating Failure of 316L Fittings
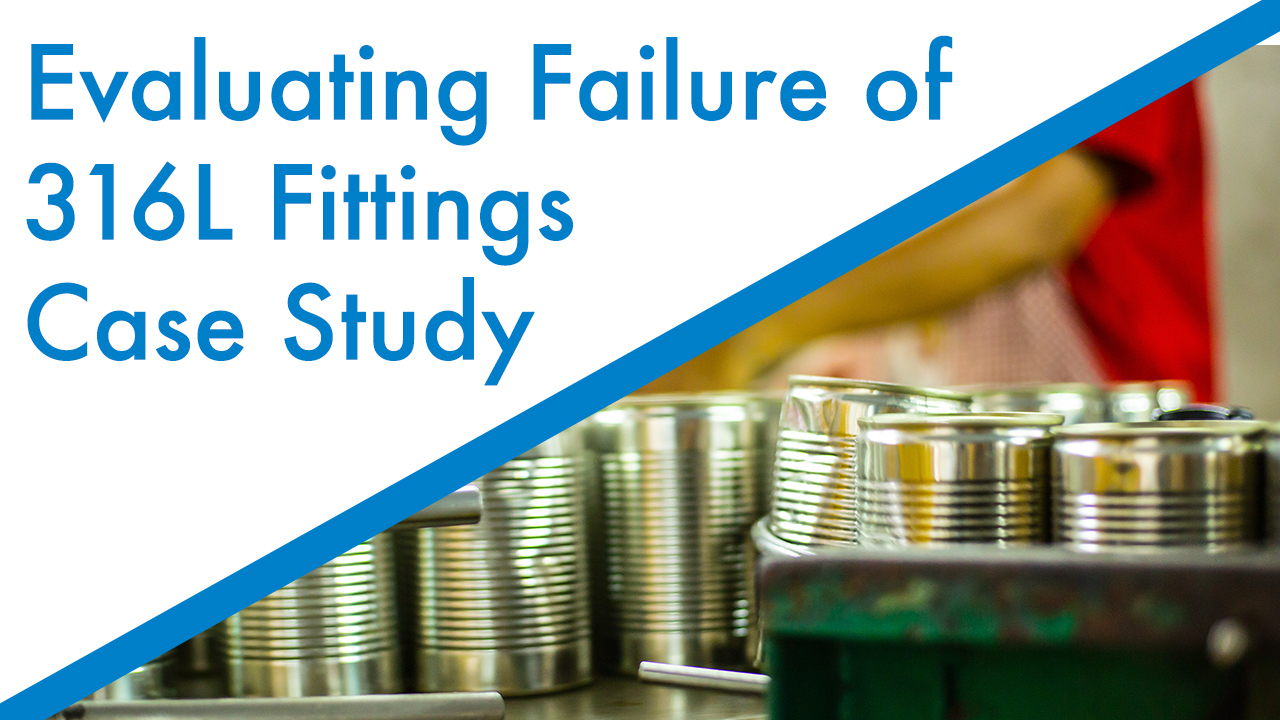
When a soup processing facility experienced leaks in their pipelines that had only been in service for four years, they turned to CSI to find out why. After a variety of tests, CSI concluded that the company should use AL-6XN, a stainless steel grade with a high molybdenum content that would stand up to the chlorides in their application.
The Cause of Pitting in 304L Tubing
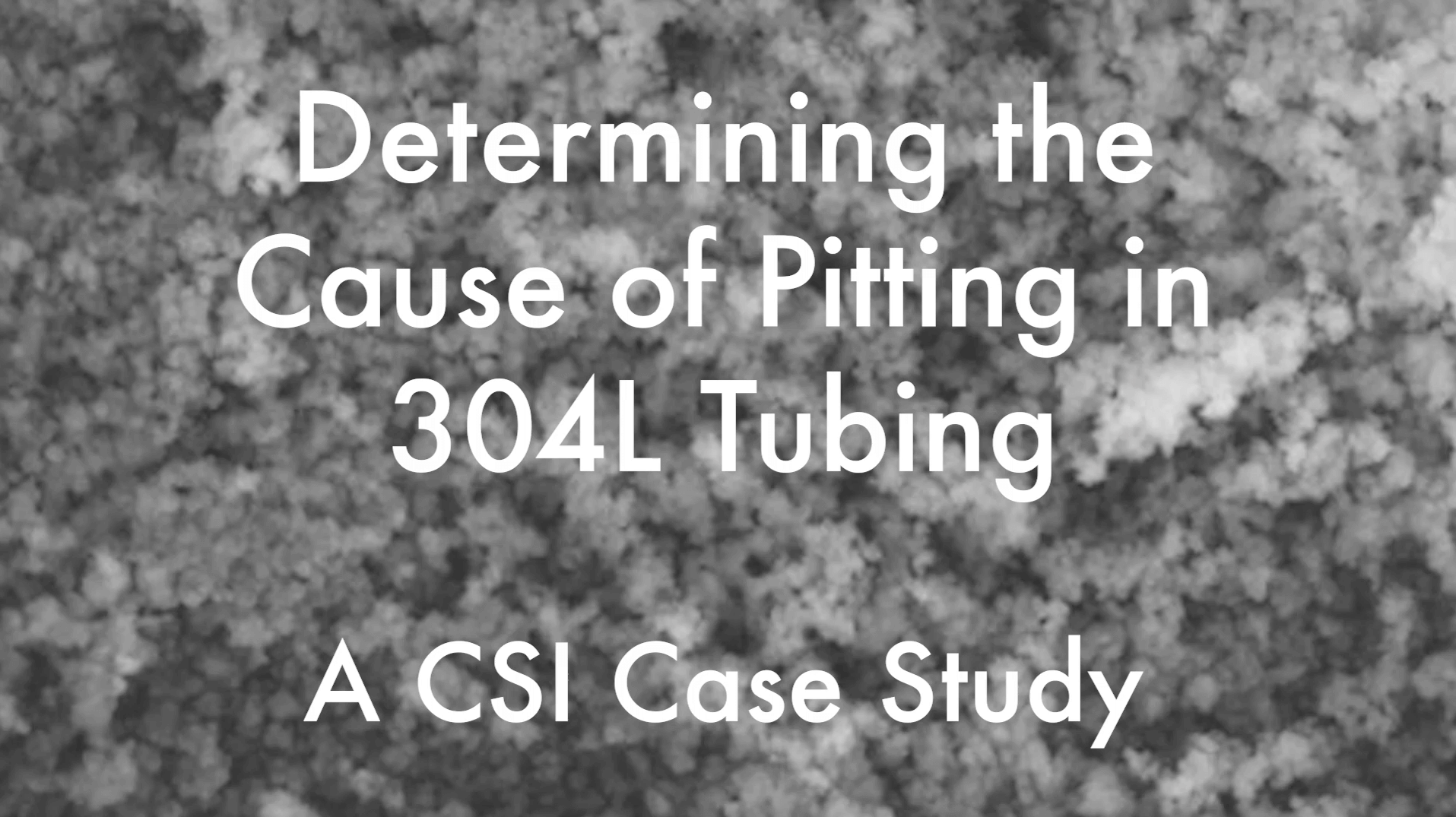
A cheese processing plant encountered corrosion in their recently installed 304L piping, they then looked to CSI to find the cause of the pits. Through a series of tests CSI recommended that the facility use a higher grade metal, AL-6XN to solve their problem with Microbial Induced Corrosion.
Literature
Literature
Create a MyCSI Dashboard to save resources for quick reference, track orders, and talk with experts.
Create a MyCSI Dashboard to save resources for quick reference, track orders, and talk with experts.
It only takes a minute.
Sign in
Sign in to save resource to your dashboard.
Literature for AL-6XN® Alloy have been saved to your dashboard!
Literature for AL-6XN® Alloy are already in your dashboard.